In the intricate world of metalworking, precision casting stands as a testament to human ingenuity and technological prowess. This ancient technique, dating back thousands of years, has undergone a remarkable transformation, merging with modern advancements to produce components with unparalleled accuracy, complexity, and performance. Today, precision casting is a vital cog in the machinery of industries ranging from aerospace to medical, automotive to oil and gas, where the demand for lightweight, durable, and highly specialized metal parts is relentless. This comprehensive exploration delves into the intricacies of precision casting, highlighting its principles, processes, benefits, and, ultimately, showcasing how Shenzhen Yujiaxin Tech. Co., Ltd. leverages this technology to craft an array of complex metal components.
The Essence of Precision Casting
Precision casting, also known as investment casting or lost-wax casting, is a process that involves creating a replica of a desired component in wax or a similar material. This pattern, known as the “master pattern,” serves as the blueprint for the final metal part. The pattern is then coated with several layers of a refractory material (such as ceramic slurry), which hardens to form a shell, encasing the wax pattern. Once the shell is sufficiently strong, the wax is melted and removed, leaving behind a hollow mold that accurately reflects the shape and dimensions of the original pattern.
The next step involves pouring molten metal into this mold, where it cools and solidifies, taking on the precise form of the original design. Upon cooling, the ceramic shell is broken away, revealing the cast metal component. This entire process requires meticulous attention to detail, precise temperature control, and the use of high-quality materials to ensure the final product meets or exceeds the desired specifications.
Processes and Techniques
Precision casting encompasses various sub-processes and techniques, each tailored to specific applications and material requirements. Some of the key processes include:
Pattern Making: The initial step involves creating an accurate wax or plastic pattern that serves as the basis for the casting. Modern CAD/CAM technology allows for precise design and rapid prototyping, facilitating the creation of complex geometries that would be difficult or impossible to achieve with traditional methods.
Shell Formation: The pattern is then coated with multiple layers of refractory material to form a strong, insulating shell. This shell must be able to withstand the high temperatures of the molten metal without cracking or deforming, ensuring a smooth and accurate casting.
Dewaxing: Prior to pouring the metal, the wax pattern is removed from the shell through a controlled melting process. This step requires careful temperature control to avoid damaging the shell or leaving residual wax that could contaminate the casting.
Pouring and Solidification: Molten metal is carefully poured into the shell, filling every crevice and corner of the mold. As the metal cools and solidifies, it takes on the shape of the original pattern, resulting in a precise replica in metal form.
Shell Removal and Finishing: Once the metal has fully solidified, the ceramic shell is broken away, revealing the cast component. Final finishing operations, such as cutting, grinding, and polishing, may be necessary to achieve the desired surface finish and dimensional accuracy.
The Material Diversity of Precision Casting: Exploring the Versatility and Properties of Cast Metals
Precision casting, a testament to human ingenuity and technological advancement, stands out as a manufacturing process that transcends traditional limitations, embracing a vast array of materials with diverse properties and performance characteristics. This versatility is one of the key strengths of precision casting, enabling the production of components tailored to meet the most stringent requirements across various industries. In this comprehensive exploration, we delve into the material diversity of precision casting, examining the specific materials used, their unique properties, and the performance advantages they offer.
The Spectrum of Materials for Precision Casting
Precision casting is not limited to a single metal or alloy but embraces a broad range of materials, each with its own set of strengths and applications. These materials can be broadly categorized into several groups, including stainless steels, nickel-based alloys, cobalt-chromium alloys, titanium, superalloys, and even non-ferrous metals like aluminum and copper-based alloys (albeit with certain limitations due to their melting points and casting challenges).
1. Stainless Steels
Stainless steels are a popular choice for precision casting due to their excellent corrosion resistance, high strength, and good formability. These alloys contain a minimum of 10.5% chromium, which forms a thin, passive oxide layer on the surface, protecting the metal from oxidation and corrosion. Depending on the specific grade, stainless steels can offer varying degrees of hardness, toughness, and weldability, making them suitable for a wide range of applications, including medical implants, food processing equipment, and chemical industry components.
Material Properties and Performance:
- Corrosion Resistance: The chromium oxide layer provides excellent resistance to a variety of corrosive environments, including acids, alkalis, and salts.
- Strength and Toughness: Stainless steels exhibit high tensile strength and good ductility, enabling them to withstand significant loads without failing.
- Hygiene: Non-porous and easy to clean, stainless steels are ideal for applications where hygiene is critical, such as in the food and medical industries.
2. Nickel-Based Alloys
Nickel-based alloys are renowned for their exceptional high-temperature strength, corrosion resistance, and good mechanical properties. These alloys often contain significant amounts of chromium, molybdenum, tungsten, and other elements, which contribute to their exceptional performance. Nickel-based alloys are widely used in aerospace, energy, and petrochemical industries, where components must withstand extreme temperatures, corrosive environments, and high stresses.
Material Properties and Performance:
- High-Temperature Strength: Nickel-based alloys retain their strength and ductility at temperatures far exceeding those of conventional metals, making them ideal for applications involving high-temperature exposure.
- Corrosion Resistance: The addition of chromium, molybdenum, and other elements enhances the alloys’ resistance to a wide range of corrosive media, including acids, alkalis, and salts.
- Fatigue Resistance: These alloys exhibit excellent fatigue resistance, making them suitable for components subjected to cyclic loading conditions.
3. Cobalt-Chromium Alloys
Cobalt-chromium alloys are known for their excellent wear resistance, high strength, and biocompatibility, making them a popular choice for medical implants, particularly orthopedic devices. These alloys contain a significant amount of cobalt, chromium, and sometimes molybdenum and tungsten, which contribute to their unique properties.
Material Properties and Performance:
- Wear Resistance: Cobalt-chromium alloys exhibit exceptional resistance to wear and abrasion, making them suitable for applications where long-term durability is crucial.
- Biocompatibility: These alloys are well-tolerated by the human body, with low toxicity and a minimal risk of allergic reactions, making them ideal for medical implants.
- High Strength and Hardness: Cobalt-chromium alloys offer high tensile strength and hardness, enabling them to withstand significant loads and resist deformation.
4. Titanium
Titanium is a lightweight, strong, and corrosion-resistant metal that has found widespread use in aerospace, medical, and automotive industries. Its unique combination of properties, including high strength-to-weight ratio, low density, and excellent biocompatibility, makes it an attractive material for precision casting.
Material Properties and Performance:
- Lightweight: With a density approximately 60% that of steel, titanium offers significant weight savings without compromising strength.
- High Strength-to-Weight Ratio: Titanium’s exceptional strength-to-weight ratio makes it ideal for applications where weight reduction is critical, such as in aircraft components.
- Corrosion Resistance: Titanium forms a protective oxide layer on its surface, providing good resistance to corrosion in a variety of environments.
- Biocompatibility: Similar to cobalt-chromium alloys, titanium is well-suited for medical applications due to its low toxicity
Process Flow Diagram for precision casting
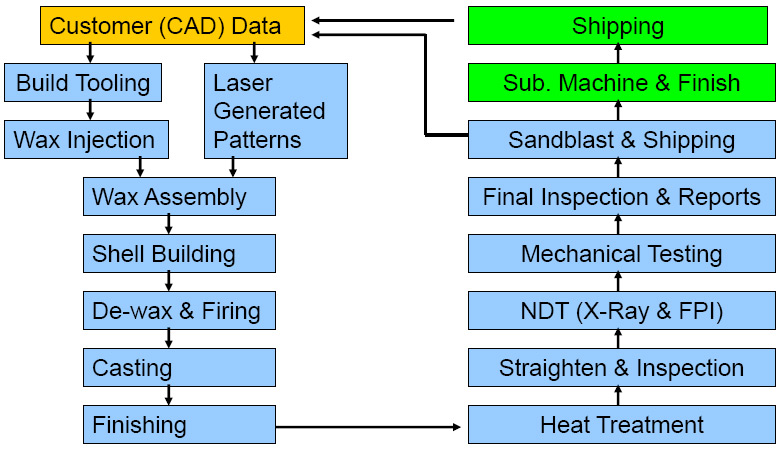
Precision Casting: A Comprehensive Analysis of Its Advantages and Disadvantages
Precision casting, also known as investment casting or lost-wax casting, is a highly sophisticated metal forming process that has been refined over centuries to meet the demands of modern manufacturing. This technique, characterized by its ability to produce complex, near-net-shape components with exceptional accuracy and repeatability, holds a prominent place in industries ranging from aerospace and automotive to medical and jewelry. However, like any manufacturing process, precision casting is not without its share of advantages and disadvantages. In this comprehensive analysis, we delve into the strengths and limitations of precision casting, providing insights into why it remains a preferred choice for many manufacturers.
Advantages of Precision Casting
1. Complex Geometry Capability
One of the primary advantages of precision casting lies in its ability to produce components with intricate geometries and fine details that would be difficult or impossible to achieve through other casting or machining processes. By utilizing a wax or plastic pattern, which is subsequently invested in a refractory material and melted out, the process allows for the creation of hollow structures and intricate internal passages with remarkable precision. This capability is particularly valuable in industries such as aerospace, where lightweight, high-strength components with complex cooling channels or internal structures are essential.
2. High Dimensional Accuracy
Precision casting offers exceptional dimensional accuracy, with tolerances that can be as tight as ±0.1% of the dimension being cast. This is achieved through a combination of factors, including the use of precise patterns, the investment process, and the controlled cooling rates during solidification. The result is a near-net-shape product that requires minimal or no post-processing, significantly reducing waste and lead times.
3. Material Versatility
Another significant advantage of precision casting is its ability to accommodate a wide range of materials, including stainless steels, nickel-based alloys, cobalt-chromium alloys, titanium, and even some non-ferrous metals like aluminum (albeit with limitations due to its low melting point). This versatility enables manufacturers to select the optimal material for their application, based on factors such as strength, corrosion resistance, weight, and cost.
4. Smooth Surface Finish
Precision casting produces components with a smooth, polished surface finish, which can often eliminate the need for additional finishing operations. This not only reduces manufacturing costs but also enhances the overall aesthetic appeal of the product, making it suitable for applications where surface quality is critical, such as in jewelry, medical implants, and high-end automotive components.
5. Repeatability
The precision casting process is highly repeatable, ensuring consistent quality from one casting to the next. This is achieved through the use of standardized patterns and processes, as well as rigorous quality control measures. This repeatability is essential in industries where reliability and performance are paramount, such as aerospace and medical device manufacturing.
Disadvantages of Precision Casting
1. High Initial Costs
One of the primary disadvantages of precision casting is the high initial cost associated with tooling and setup. The creation of precise patterns and molds can be expensive, especially for complex geometries or small production runs. Furthermore, the investment process itself, which involves multiple steps and specialized materials, adds to the overall cost. These costs can be prohibitive for some manufacturers, particularly those with tight budgets or limited production volumes.
2. Limited Production Rates
Precision casting is a relatively slow process, with production rates limited by the time required for the investment, burnout, and casting cycles. This can make it less suitable for high-volume production runs, where faster and more cost-effective processes like die casting or injection molding may be more appropriate.
3. Material Limitations
While precision casting accommodates a wide range of materials, there are still some limitations. For example, aluminum and other low-melting-point metals are difficult to cast using traditional precision casting methods due to their high thermal conductivity and low viscosity. This can lead to defects such as porosity and hot tears. Additionally, some materials may be too expensive or difficult to procure in the quantities required for precision casting.
4. Waste Generation
Precision casting generates a significant amount of waste, including the patterns, investment material, and gating systems. While much of this waste can be recycled, the process still requires careful management to minimize environmental impact and disposal costs.
5. Skill Requirements
Precision casting is a highly skilled process that requires experienced technicians to ensure consistent quality. The creation of precise patterns, the investment process, and the casting operation itself all demand a high level of expertise and attention to detail. This can make it challenging to find and retain skilled labor, particularly in regions with a shortage of experienced workers.
In conclusion, precision casting offers a unique combination of advantages and disadvantages that must be carefully considered when selecting a manufacturing process. Its ability to produce complex geometries with high dimensional accuracy, combined with material versatility and a smooth surface finish, makes it an attractive choice for many manufacturers. However, the high initial costs, limited production rates, material limitations, waste generation, and skill requirements must also be taken into account.
6. Sensitivity to Design Changes
Another potential disadvantage of precision casting is its sensitivity to design changes. Because the process relies on precise patterns and molds, any modifications to the design require the creation of new patterns and molds, which can be time-consuming and expensive. This can make precision casting less suitable for projects where frequent design iterations are expected.
7. Potential for Defects
Despite its many advantages, precision casting is not without its risks of defects. Common issues include porosity (the presence of tiny holes or voids in the casting), shrinkage cavities (voids caused by insufficient material during solidification), and surface defects such as cracks, blisters, or rough spots. These defects can be caused by a variety of factors, including impurities in the metal, inadequate venting, and improper cooling rates. To minimize the risk of defects, manufacturers must carefully control the casting process and employ rigorous quality control measures.
8. Environmental Impact
Finally, the environmental impact of precision casting must be considered. While the process itself is generally considered environmentally friendly, the generation of waste materials and the potential for air and water pollution during the casting and finishing operations must be managed responsibly. Manufacturers must ensure compliance with relevant environmental regulations and strive to minimize their environmental footprint through recycling, waste reduction, and the use of sustainable materials and practices.
In summary, precision casting is a highly sophisticated manufacturing process that offers numerous advantages, including the ability to produce complex geometries with high dimensional accuracy, material versatility, and a smooth surface finish. However, it is not without its limitations, including high initial costs, limited production rates, material restrictions, waste generation, skill requirements, sensitivity to design changes, potential for defects, and environmental impact. Manufacturers must carefully evaluate these factors when deciding whether precision casting is the right process for their application. By doing so, they can leverage the strengths of precision casting while mitigating its potential drawbacks, resulting in high-quality, cost-effective products that meet the demands of today’s competitive marketplace.