In the vast field of manufacturing, there are a variety of manufacturing processes to choose from, whether it is the production of small precision components or large structural components. The choice of these processes often depends on the comprehensive consideration of raw material characteristics, product design requirements, cost-effectiveness and material applicability. Among them, die casting and metal injection molding (MIM)
As two mainstream technologies, each has unique advantages and application areas, and usually complements rather than replaces each other.
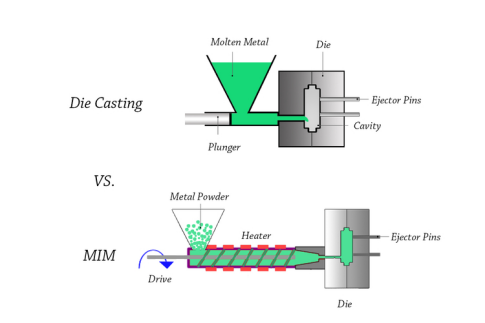
-Metal Injection Molding: The Art of Precision Manufacturing
Metal injection molding is an advanced technology that uses traditional injection molding equipment to produce small and complex metal parts. These parts show excellent strength, durability and wear resistance, especially for geometric designs that require thin-walled structures. MIM technology not only meets customers’ high requirements for precision and complexity, but also maximizes cost-effectiveness through the following ways:
- Efficient mass production: ensure consistent part quality.
- Reduce material waste: optimize material utilization.
- Reduce secondary processing: parts are close to the final shape, reducing subsequent processing costs.
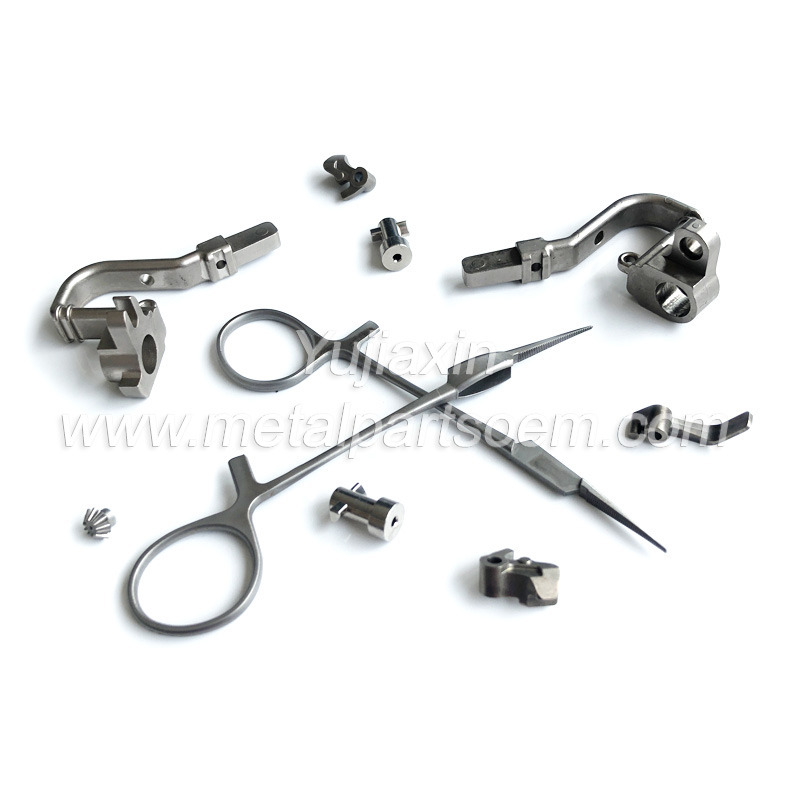
-Die casting: Exquisite craftsmanship for efficient replication
Die casting is a technology that uses a mold to inject and cool molten non-ferrous metal into a mold, which can mass-produce parts with high durability and complex structures while maintaining a high degree of consistency in the original design specifications. The design of die casting molds is flexible and diverse, including single-cavity molds, combination molds, unit molds and multi-cavity molds to meet the manufacturing needs of parts with different shapes and internal structures.
The choice of die casting process is often based on its simple and efficient characteristics, which can quickly inject molten metal into the mold and cool it to form, thereby achieving rapid replication of parts. According to the process characteristics, die casting can be subdivided into three types: gravity die casting, cold die casting and hot die casting, each of which has its specific application scenarios and advantages.
-Comparative analysis of die casting and metal injection molding
When comparing die casting and metal injection molding, the following five aspects are particularly significant and will directly affect the choice of which process is more suitable for a specific project:
1. Precision and tolerance: MIM can produce precision parts with extremely small tolerance ranges, while die castings may have certain dimensional variations and require subsequent finishing.
2. Material applicability: MIM technology is suitable for a variety of metal materials, including ferrous metals, while die casting mainly uses non-ferrous metals.
3. Surface treatment: Die castings may require additional finishing to achieve a medium surface finish, while MIM parts generally have a high surface finish, reducing the need for subsequent processing.
4. Cost and tooling: Although MIM is less expensive in mass production, its process cost is relatively high. Depending on part complexity and specific application, die casting may be more cost-effective in some cases.
5. Mold design and life: MIM provides greater flexibility in mold design, but the mold life may be shorter; while die casting molds generally have a longer life, although the flexibility is slightly less than MIM.
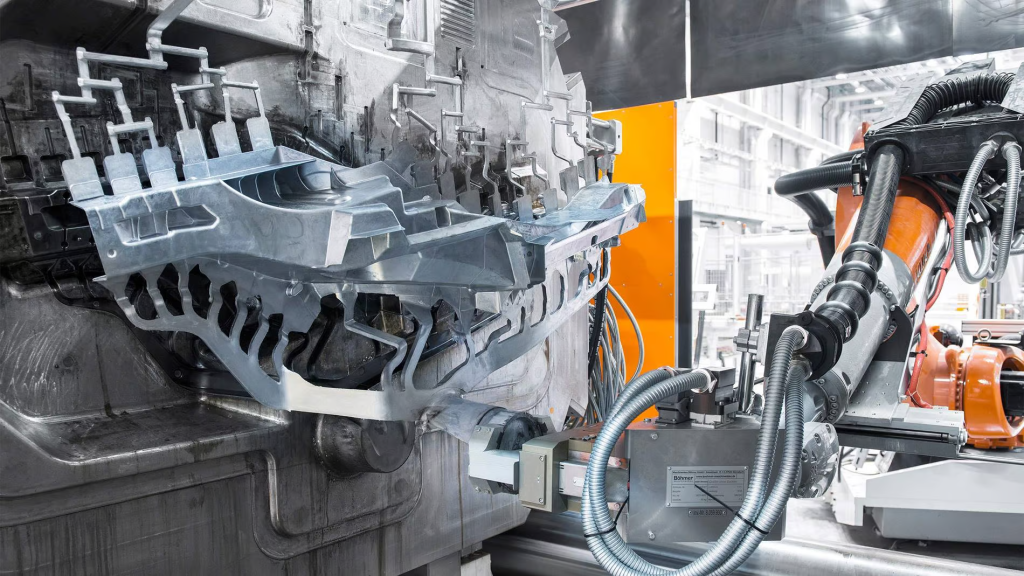
When deciding which manufacturing process to use, it is necessary to consider product design, material requirements, cost-effectiveness, and the end use of the part. MIM may be an ideal choice for parts that require high precision, complex structures, and thin-walled designs; while die casting is more advantageous for parts that pursue efficient production, cost optimization, and large-scale replication.
For more detailed information on metal injection molding and die casting technology, please consult Yujiaxin’s team of experts to start your next manufacturing project. Shenzhen Yujiaxin Technology Co., Ltd. has been deeply involved in the field of metal powder injection molding for many years and specializes in the production of various high-precision complex structure metal parts. Our products are widely used in many fields such as medical equipment accessories, military parts, surgical instrument parts, such as surgical graspers, tweezers, surgical blades, ultrasonic blades, laparoscopic forceps, endoscope parts, etc. At the same time, we also provide sports equipment accessories, electrical hardware parts, etc. to meet the needs of different industries.
Yujiaxin Technology, with excellent quality and professional technology, provides you with a one-stop metal parts solution!