MIM (Metal Injection Molding) 4340 material is a high-strength, high-performance alloy steel widely used in many industrial fields. This article will give a detailed introduction to the chemical composition, mechanical properties, application fields and heat treatment process of MIM 4340 material.
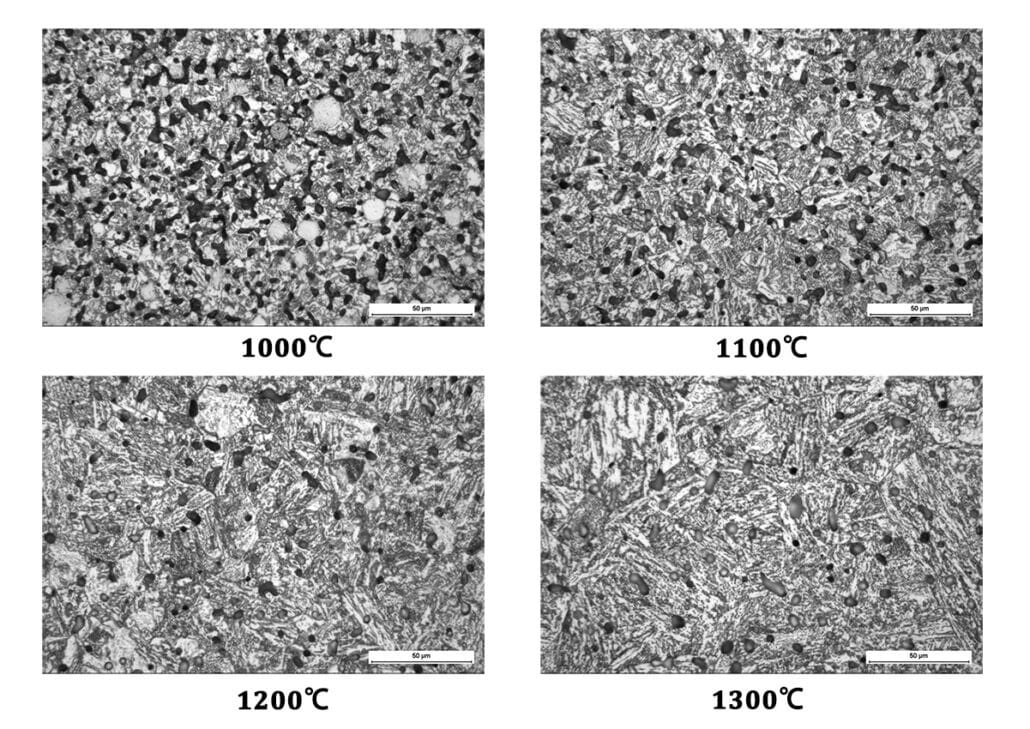
Chemical composition and mechanical properties
MIM 4340 material is a medium-carbon nickel-chromium-molybdenum steel alloy containing appropriate amounts of carbon, silicon, manganese, sulfur, phosphorus, chromium, nickel, copper and molybdenum. These elements together give 4340 material excellent tensile strength, toughness and fatigue resistance. Specifically, the standard carbon content of 4340 material ranges from 0.38% to 0.43% (mass fraction), and the carbon content in this range helps to achieve the best mechanical properties.
In addition to carbon, other alloying elements also play an important role. For example, chromium and nickel elements improve the corrosion resistance and toughness of the material, while molybdenum further enhances its fatigue resistance. These alloying elements enable 4340 material to maintain excellent performance in a variety of harsh environments.
In terms of mechanical properties, MIM 4340 material performs well. Its tensile strength, yield strength, elongation and hardness have all reached a high level. For example, in some studies, through specific heat treatment processes, these performance data show that MIM 4340 material has extremely high reliability and stability when subjected to heavy loads and complex stress environments.
Application Fields
MIM 4340 material is widely used in multiple industrial fields due to its excellent performance.-In the field of heavy machinery, 4340 material is often used to manufacture transmission parts such as heavy shafts, gears and axles.
- In the military industry and commercial aircraft industry, it is used to manufacture key structural parts such as landing gear, engine components and fuselage frames due to its high strength and fatigue resistance.
- In automobile manufacturing, it is used to manufacture key components such as transmission systems, suspension systems and steering systems.
- In the field of heavy machinery, 4340 material is often used to manufacture transmission parts such as heavy shafts, gears and axles.
- In the field of rocket engines, it is used to manufacture components such as combustion chambers, turbine blades and nozzles due to its high temperature strength and corrosion resistance.

Heat treatment process
Heat treatment is a very critical step for MIM 4340 material. Through heat treatment methods such as normalizing, oil quenching and tempering, the mechanical properties of the material can be further improved, and its strength and fatigue resistance can be increased.
During the normalizing process, the material is heated to above the critical temperature and maintained for a period of time, and then air-cooled or air-cooled. This step helps to eliminate the structural defects in the material and improve its overall performance. Oil quenching is to quickly immerse the material heated above the critical temperature in cooling oil to quickly cool and obtain martensitic structure. This step significantly improves the hardness and strength of the material.
Tempering is to heat the material to a certain temperature after quenching and maintain it for a period of time, and then cool it. This step helps to eliminate quenching stress and improve the toughness and plasticity of the material. According to different application requirements, different tempering temperatures and times can be selected to obtain the required mechanical properties.
In recent years, research on MIM 4340 materials has made significant progress. Researchers have further optimized the microstructure and mechanical properties of MIM 4340 materials by adjusting parameters such as carbon content, sintering temperature and heat treatment process. For example, by adding reduced carbonyl iron powder (CN) and improved carbonyl iron powder (OM) from BASF, mixed powders with different carbon contents can be formulated, and the best mechanical properties can be obtained through specific sintering and heat treatment processes.
These research results provide strong support for the application of MIM 4340 materials in a wider range of fields. In the future, with the continuous development of materials science and manufacturing technology, MIM 4340 materials are expected to play an important role in more fields.
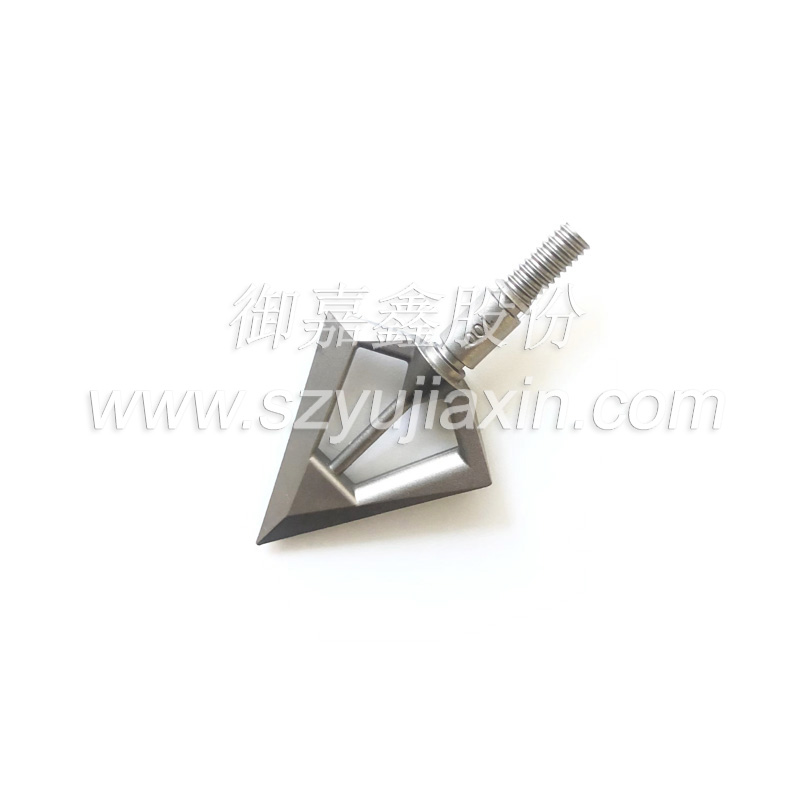
Shenzhen Yujiaxin Technology Co., Ltd., as a leader in the field of metal injection molding (MIM), we focus on providing excellent metal parts solutions for the medium and high-demand markets. Relying on advanced MIM technology, we can accurately process metal parts with complex structures, extremely high precision and stable performance, which are widely used in high-end fields such as communications, medical, automobiles, aerospace, etc. Yujiaxin adheres to the spirit of craftsmanship and continuously optimizes the process to ensure that every product can meet the most stringent quality standards of customers. We are committed to becoming a trusted partner of customers, jointly promoting industrial upgrading, and opening a new chapter in metal parts processing.