1.Basic principles of powder metallurgy
Powder production methods
Atomization method: This method uses high-speed airflow, water flow or centrifugal force to disperse molten metal into fine droplets and quickly cool and solidify to form powder. It is widely used in the production of powders of iron, steel, stainless steel, copper, aluminum and their alloys. The advantage of the atomization method is that it can produce spherical powders with uniform particle size and regular shape, which is conducive to subsequent forming and sintering processes. However, the equipment cost is high and the energy consumption is large.
Mechanical alloying method: Mix a variety of metal powders or metal and non-metal powders through high-energy ball milling, and use mechanical force to make them react in the solid state to generate new alloys or composite materials. It is suitable for the preparation of refractory metals and alloys. However, the process is complicated, the cycle is long, and the equipment requirements are high.
2.Powder morphology, particle size and its impact on subsequent processes
Powder morphology and particle size are key factors affecting powder metallurgy. Spherical powder has good fluidity and filling properties, and is suitable for pressing and injection molding processes. Irregularly shaped powders may enhance the mechanical bite force between powders, which helps to improve the strength of sintered materials. The particle size distribution of the powder directly affects the density and uniformity of the material. Fine powder can improve the density of the sintered body, but too fine powder can easily lead to agglomeration or separation problems during the forming process.
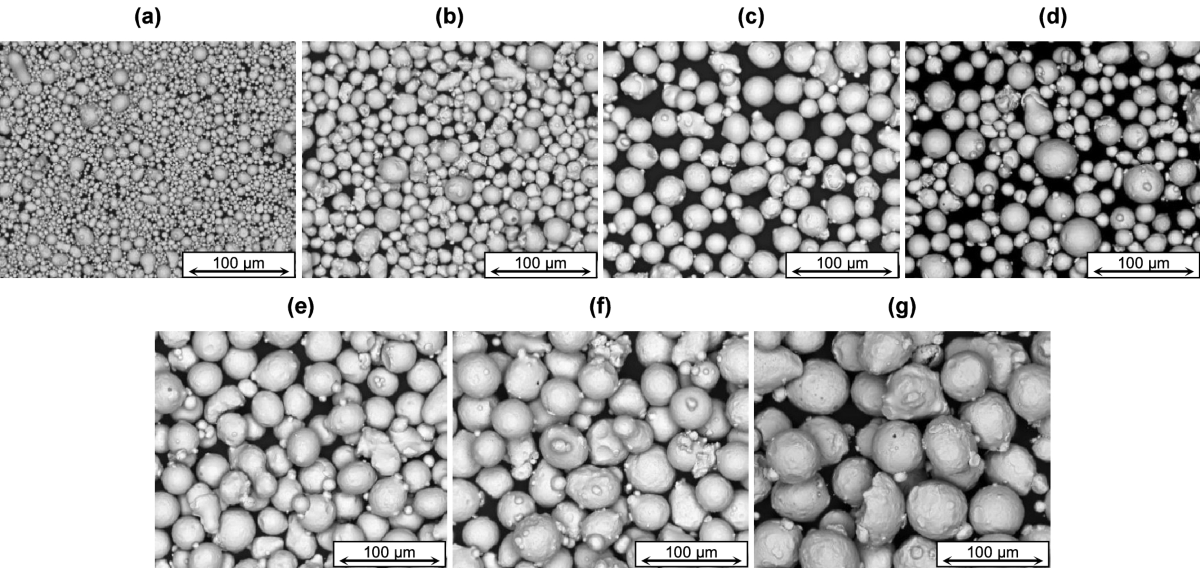
3.Forming process Pressing forming process
Cold pressing: Pressing metal powder into a mold at room temperature, commonly used for powder metallurgy products of iron, copper, aluminum and their alloys. The process is simple and the cost is low, but the pressing pressure is high, and stress concentration and pores are easily generated inside the product
Hot pressing: Pressing and forming under heating conditions, the temperature is usually lower than the recrystallization temperature of the powder material. It can reduce the forming pressure, improve the compressibility of the powder, and improve the density and strength of the formed body.
Isostatic pressing: including cold isostatic pressing (CIP) and hot isostatic pressing (HIP), which realizes the dense forming of powder by uniformly applying pressure in all directions. A highly uniform and dense material structure can be obtained, which is suitable for the preparation of complex shapes and high-performance materials.
Injection molding process
Injection molding process (Powder Injection Molding, PIM), including metal powder injection molding (MIM) and ceramic powder injection molding (CIM). By mixing metal or ceramic powder with an organic binder to form a feed, the feed is then injected into the mold through an injection molding machine to form. It can produce small parts with complex shapes and high dimensional accuracy, with high production efficiency and suitable for mass production.
The influence of forming process on material properties
The forming process directly affects the density, strength, dimensional accuracy and surface quality of powder metallurgy products. High-pressure pressing and isostatic pressing can obtain high-density and high-strength materials, but may cause stress concentration and dimensional deformation problems. The injection molding process can achieve complex shapes and high dimensional accuracy, but attention should be paid to the removal of binders and volume shrinkage during sintering.
4.Efficient utilization of materials in powder metallurgy process
The powder metallurgy process has demonstrated significant advantages in terms of material utilization. Compared with traditional casting and machining methods, these methods are often accompanied by the removal of a large amount of redundant materials, while powder metallurgy achieves the goal of near net forming with precise powder molding and sintering steps, greatly reducing material loss. In this process, the raw powder is directly pressed into a blank close to the final form, and then sintered to achieve the final densification and performance improvement. The material utilization rate can usually rise to more than 95%. This feature not only effectively saves material costs, but also reduces the burden of waste treatment and recycling during the production process. In addition, powder metallurgy technology also has the ability to recycle and reuse scraps and waste powder in the production process, further improving the efficiency of material use. For example, the waste powder generated in the manufacturing process can be put into the production process again after screening and re-proportioning, forming a closed-loop recycling system.
5.Green and environmentally friendly characteristics of the process
The powder metallurgy process has shown outstanding advantages in environmental protection, which is specifically reflected in the following aspects:
Waste reduction: Due to the high material utilization rate of the process, the amount of waste generated during the production process is greatly reduced, which not only reduces the cost and challenges of waste treatment, but also reduces environmental pollution.
Reduced energy consumption: Compared with traditional casting and forging processes, the forming and processing energy required for powder metallurgy is relatively low. For example, the energy consumption of preparing powder by atomization is significantly lower than that of smelting and casting, and the energy consumption of the sintering stage is also relatively low.
Reduced harmful emissions: During the production process, especially in the sintering process where the atmosphere is controlled, the harmful gas emissions of the powder metallurgy process are much lower than those of traditional metallurgical processes. The use of inert gas or vacuum environment can further inhibit the occurrence of oxidation and other harmful chemical reactions.
Utilization of industrial waste: The process can also effectively utilize industrial waste and by-products. By crushing and screening industrial waste, metal powder that meets the standards can be produced, realizing the transformation of waste into valuable raw materials.
Shenzhen Yujiaxin Technology Co., Ltd. focuses on customizing and processing parts according to drawings, and is committed to providing customers with high-quality and efficient customized services.