1.High performance and complex shape implementation
High uniformity and density of materials
The powder metallurgy process has unparalleled advantages in the uniformity and density of materials. By precisely controlling the composition, morphology and particle size of the powder, materials with a highly uniform structure can be produced. The powder particles are evenly distributed during the pressing and sintering processes, avoiding component segregation and structural unevenness that are common in traditional casting processes.
High density is a highlight of powder metallurgy products. By optimizing the forming pressure and sintering conditions, the density of the product can be significantly improved, the porosity can be reduced, and the mechanical properties and durability of the material can be enhanced. High-density materials have excellent performance in strength, hardness, fatigue resistance, etc., and are suitable for high-stress and high-load environments.
2.Manufacturing capabilities of complex shapes and microstructures
The powder metallurgy process is particularly good at manufacturing parts with complex shapes and fine structures, which are often difficult to achieve in traditional metallurgical processes. The specific performance is as follows:
Complex geometric shapes: Through mold forming, powder metallurgy technology can produce parts with complex geometric shapes that are difficult to achieve with traditional processes, such as internal channels, small holes, and complex curved surfaces. This is ideal for high-precision and complex structural parts (such as aerospace parts, medical parts, etc.) implants, etc.) are crucial.
Microstructure: This technology can create micron-scale or even nano-scale fine structures, showing unique advantages in the preparation of high-performance functional materials (such as magnetic materials, catalyst materials, etc.). By controlling the particle size and sintering parameters of powder particles, precise control and optimization of the microstructure can be achieved.
Near net shape: The near net shape characteristic of the powder metallurgy process allows parts to meet final use requirements with only a small amount or no finishing after forming, which not only saves time and cost, but also improves material utilization.
3.Realization of versatility and comprehensive performance
The powder metallurgy process combines composite forming with multiple materials to create parts with versatility. For example, metal-ceramic composite materials, metal-polymer composite materials, etc., through this technology, the organic combination of different material properties can be achieved to achieve comprehensive performance that is difficult to achieve with a single material.
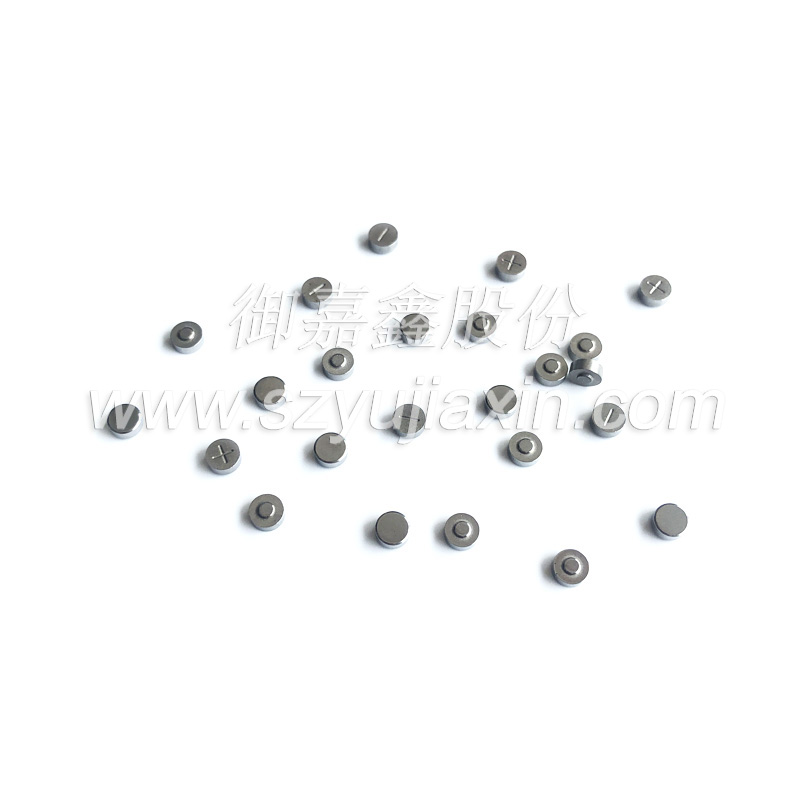
4.Development of special materials and functions
Diversity of alloy materials and design freedom
Powder metallurgy technology provides a broad space for material design. By accurately controlling the composition and proportion of powders, a variety of new alloy materials can be developed. The specific performance is as follows:
High-performance alloys: This technology can produce alloy materials with excellent properties, such as high-temperature alloys, corrosion-resistant alloys and high-strength alloys, which are widely used in aerospace, energy, chemical industry and other fields.
Complex composition alloy: Through mechanical alloying or mixed alloying technology, a variety of metal powders can be mixed to prepare alloy materials with complex and uniform composition. For example, some high-temperature alloys and superhard alloys have complex compositions and strict requirements. The uniform distribution and precise control of the compositions can be achieved through powder metallurgy technology.
Gradient functional materials: This technology can also produce gradient functional materials, that is, the composition and structure of the material gradually change along the thickness direction to meet the performance requirements of different parts. Such materials are valuable in applications that require special property gradients (such as turbine blades, cutting tools, etc.).
5.Manufacturing of functional materials
The powder metallurgy process shows great potential in the manufacture of functional materials. The following are some typical functional materials and their powder metallurgy preparation methods:
Magnetic materials: Through this technology, high-performance magnetic materials can be prepared, such as NdFeB permanent magnet materials and soft magnetic materials. These materials are widely used in motors, sensors and electronic devices. Powder metallurgy technology can precisely control the composition and microstructure of magnetic materials and optimize their magnetic properties.
Thermoelectric Materials: Thermoelectric materials can convert temperature differences into electrical energy or vice versa, and can be used to generate electricity or refrigeration. By finely controlling the composition and structure of materials, powder metallurgy technology can prepare materials with excellent thermoelectric properties, such as bismuth-antimony alloys and silicon-germanium alloys, which are widely used in the fields of energy conversion and electronic cooling.
Wear-resistant materials: Wear-resistant materials such as tungsten carbide and silicon nitride can achieve a combination of high hardness and high wear resistance through powder metallurgy technology, and are widely used in cutting tools, abrasive tools, wear-resistant parts and other fields. By optimizing the morphology and sintering parameters of powder particles, the wear resistance and service life of the material can be significantly improved.
Catalytic materials: Through powder metallurgy technology, nanoscale catalysts with high surface area and excellent catalytic activity can be prepared. These materials have important applications in the chemical industry, environmental protection and energy fields, such as automobile exhaust catalysts and fuel cell catalysts.
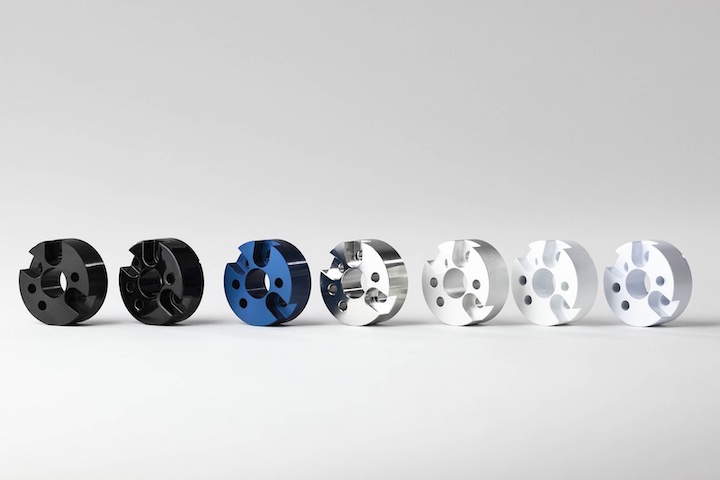
6.Manufacturing of composite materials
The powder metallurgy process can also be used to manufacture a variety of composite materials. These materials obtain comprehensive properties that are difficult to achieve with a single material through the organic combination of different components. For example:
Metal-ceramic composite materials: By mixing metal powder and ceramic powder, powder metallurgy technology can be used to produce composite materials with high strength, high hardness and high wear resistance. These materials are widely used in cutting tools, wear-resistant parts and high-temperature structural parts.
Metal-polymer composite materials: Through this technology, metal powders and polymer materials can be combined to prepare composite materials with excellent mechanical properties and special functions. For example, metal-polymer composites used in medical devices combine the strength of metal with the biocompatibility of polymers.
Functionally graded materials: Powder metallurgy technology can also prepare functionally graded materials with gradient composition and gradient structure. This material is valuable in applications that require different performance requirements in different parts (such as thermal barrier coatings, gradient structural parts, etc.).