Cemented carbide, a high-performance alloy material, is forged by ingeniously combining the hard compound of refractory metal with the bonding metal through a precise powder metallurgy process. It not only has excellent hardness and wear resistance, but also occupies an important position in the field of precision parts processing. Among them, the ingenious combination of carbide and bonding metal constitutes the unique performance advantage of cemented carbide.
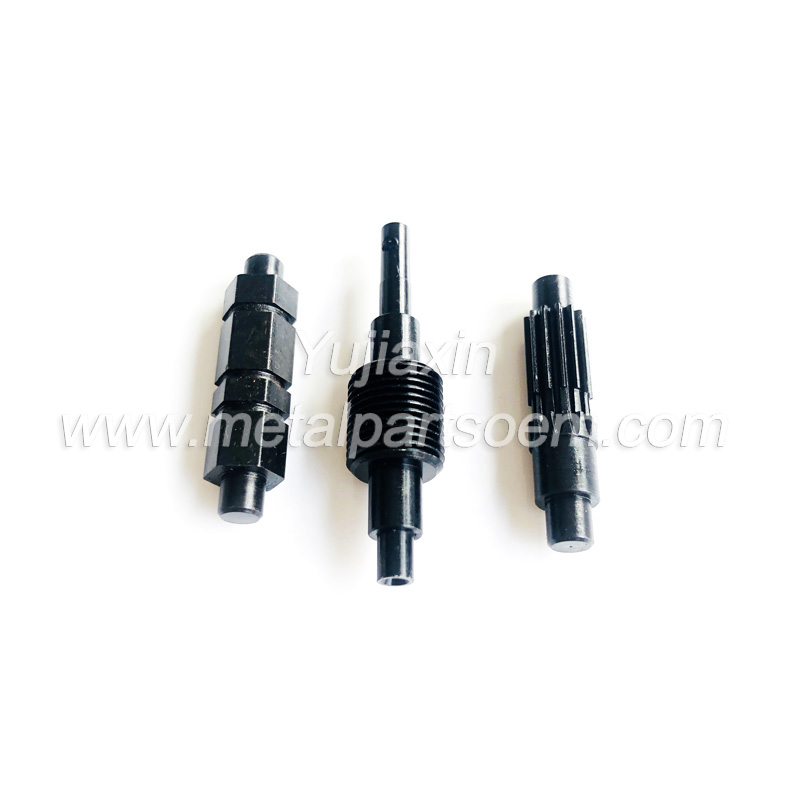
In the processing of cemented carbide, cutting is a crucial link. For cemented carbide materials in different forms such as bars, plates, and wires, the choice of cutting method is particularly important. For grooving or cutting tasks below 1mm, diamond ultra-thin cutting blades have become the preferred tool for processors due to their sharp edges and excellent wear resistance. Diamond resin-based cutting blades, with their unique structural design and excellent performance, are widely used in grooving and cutting operations with medium and large cutting depths.
In the turning process of cemented carbide, the choice of tool is also crucial. Due to the extremely high hardness of cemented carbide, the hardness of the tool must be higher than that of the workpiece to ensure the smooth progress of the processing process. At present, the tool materials for turning carbide parts are mainly high-hardness, high-heat-resistant non-metallic binder CBN and PCD (diamond). These two tool materials are not only high in hardness and good in wear resistance, but also excellent in high temperature resistance, which can meet the various stringent requirements in the carbide processing process.
For carbide parts with different hardness, the choice of tools also needs to be different. For carbide parts with a hardness less than HRA90, CBN tools made of BNK30 material have become the preferred tool for large-allowance turning due to their excellent hardness and wear resistance. For carbide parts with a hardness greater than HRA90, PCD tools made of CDW025 or resin-bonded diamond grinding wheels are often used for grinding.

In addition, in the process of machining carbide precision parts, for groove processing above R3, as well as special shapes such as the crescent groove of the roll, it is also necessary to select suitable tools for processing. The application of advanced tools such as CVD diamond-coated milling cutters and diamond-insert milling cutters not only improves processing efficiency and product quality, but also replaces traditional electrolytic corrosion and electric spark processes to a certain extent, providing a more efficient and environmentally friendly solution for the precision processing of cemented carbide.