Powder Metallurgy Injection Molding (MIM) has become one of the key processes for manufacturing precision parts due to its excellent mechanical properties, such as high strength and hardness. However, the impact resistance of parts is not fixed, but is affected by a combination of material selection, design details, molding process and post-processing.
In terms of material selection, MIM technology can cover a variety of metals and alloys, including stainless steel, titanium alloy, nickel alloy, etc., each of which exhibits unique impact resistance. For example, stainless steel and nickel-based alloys are particularly suitable for those occasions with strict requirements for high strength and high toughness due to their excellent toughness and impact resistance. In contrast, although tungsten alloy or titanium alloy has excellent hardness and extraordinary strength, it may be slightly inferior in impact resistance due to its relatively large brittleness.
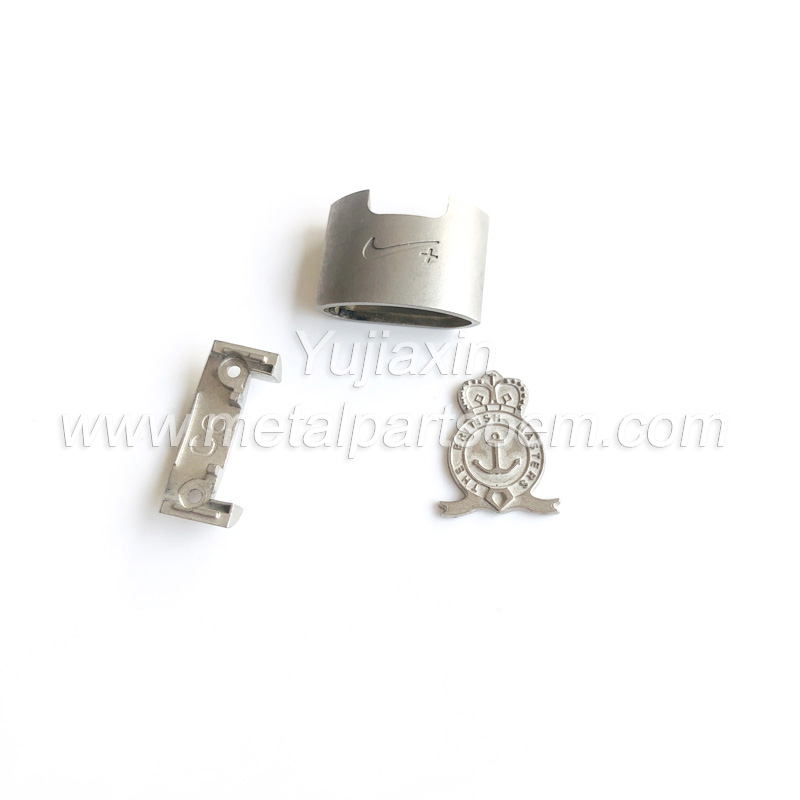
In terms of density and compactness, MIM parts can achieve a level close to the theoretical density through finely controlled densification during the sintering process. This high density is crucial to improving the impact resistance of parts, because materials with fewer internal pores can more effectively resist external impact.
In addition, the impact resistance of a part is closely related to its design. Complex shapes and thin-walled designs may weaken the performance of a part when subjected to impact. Therefore, by optimizing the geometry and wall thickness of the part, its impact resistance in practical applications can be significantly improved.
In terms of post-processing, MIM parts usually undergo a series of processes such as heat treatment and surface treatment, which help to improve the toughness and impact resistance of the material. For example, through heat treatment processes such as quenching and tempering, the toughness and strength of the part can be significantly improved, thereby enhancing its ability to withstand impact loads.

In summary, under appropriate conditions, parts manufactured by MIM technology are fully capable of meeting the impact resistance requirements of a variety of industrial applications, such as automotive parts, tools, and high-strength mechanical parts. If further improvement in impact resistance is required, designers need to pay close attention to material selection and design optimization, and may need to use additional post-processing processes to enhance the toughness and impact resistance of the part.