Metal injection molding (MIM) technology has demonstrated outstanding capabilities in the manufacturing of precision small modulus gears, and is particularly good at coping with the challenges of micro gears with complex shapes and extremely high precision requirements. Next, let’s take a closer look at the highlights of MIM technology in small gear manufacturing:
Complex shapes, easy to control
MIM technology, with its unique process, can accurately inject and mold small gears with complex structures in one go, effectively avoiding cumbersome subsequent processing procedures. This is undoubtedly a great blessing for small gears that are difficult to reach with traditional machining methods, greatly reducing the difficulty and cost of manufacturing
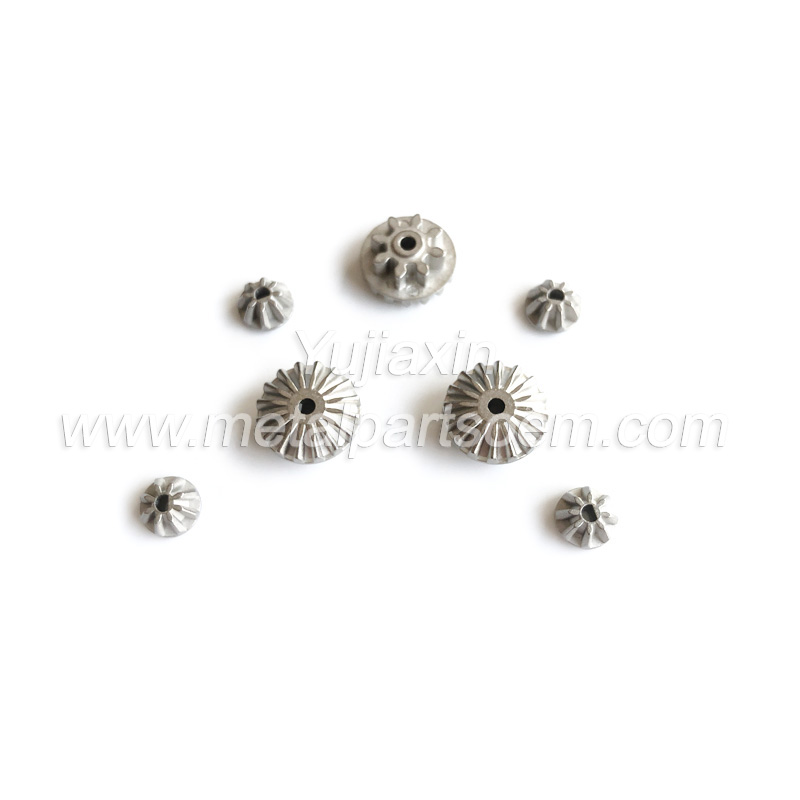
Micron-level precision, near-zero error
MIM technology performs exceptionally well in precision control, and is particularly good at producing small gears with extremely strict tolerance requirements. Its precision can easily reach the micron level, which is undoubtedly an ideal choice for gears that require precise meshing, and perfectly meets the needs of high precision.
Excellent material performance, durable and worry-free
MIM technology can create high-strength small gears with excellent mechanical properties such as hardness, wear resistance and strength. Whether it is stainless steel, alloy steel or other metal materials, they can be fully utilized through MIM technology to ensure that the gears still maintain excellent durability and wear resistance in long-term use.
Efficient production, reduced costs
MIM technology is particularly suitable for large-scale production of pinions. Its molds are highly durable and the production speed is fast, which greatly improves production efficiency and reduces production costs. This is undoubtedly a huge advantage for fields that require a large number of pinions.
Wide application areas and unlimited potential
Pinions are widely used in fields with extremely high requirements for size and precision, such as precision transmission devices, instruments and meters, electronic equipment, micro motors and clocks. With its excellent performance, MIM technology perfectly meets the high requirements for parts in these fields, especially in the fields of electronic consumer products, automotive transmission systems and medical equipment, where the demand for pinions is particularly strong.
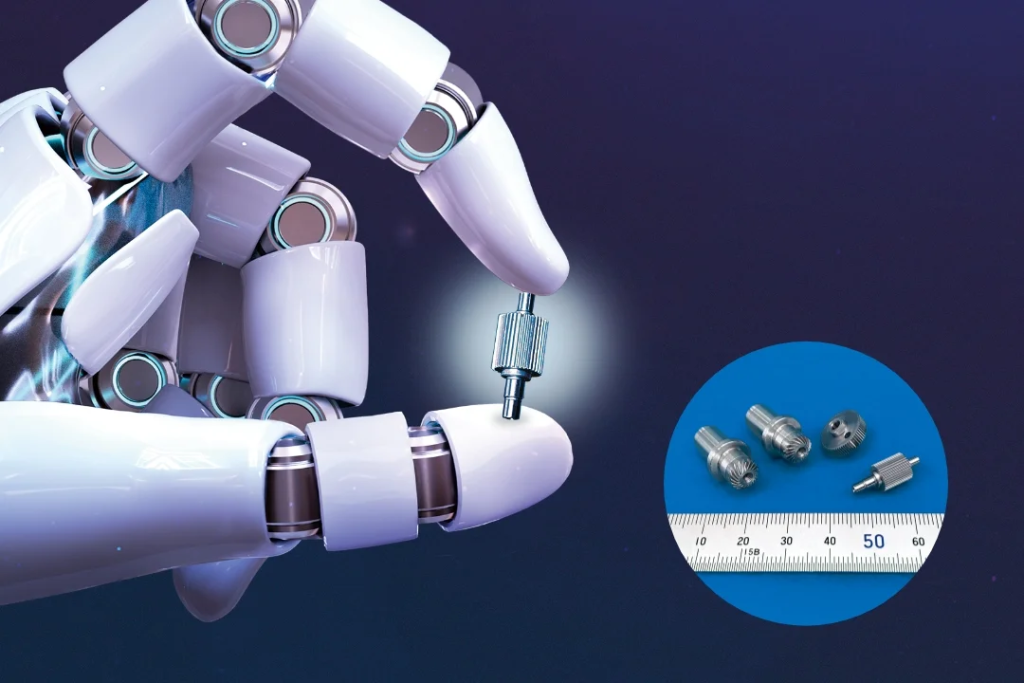
Technical challenges, overcome one by one
Although MIM technology faces challenges such as mold design and sintering process when manufacturing pinions, such as the small gear modulus leading to high mold manufacturing precision requirements, and the need to prevent deformation, shrinkage and porosity during sintering. However, with the continuous advancement of technology, these problems have been gradually overcome, and the gears produced are not only high-precision, but also stable and reliable in performance.
In summary, MIM technology provides an efficient, precise and low-cost solution for the manufacture of small gears, especially for small gears that require high strength and complex shapes. In high-end manufacturing fields such as automobiles, aerospace, medical devices and consumer electronics, the application prospects of MIM technology are extremely broad and the potential is unlimited.