In the scope of powder metallurgy, the particle size of metal powder plays a key role in determining the performance of the final product and the quality of the processing technology. Faced with diverse application scenarios, the demand for metal powder particle size also varies, which requires us to carefully select the most suitable particle size range based on the uniqueness of the process, the high standard requirements of product performance and the specific type of molding method. The following is the relevant content about metal powder particle size after sorting and editing:
1. Metal powder particle size range
The particle size of metal powder used in powder metallurgy is usually between 1 micron and 150 microns. The specific particle size selection depends on the requirements of the manufacturing process and the final product:
Coarse-grained powder (50-150 microns): suitable for larger parts or products that require high permeability and lower density.
Medium-grained powder (10-50 microns): commonly used in the manufacture of most powder metallurgy parts. This type of powder particle size can provide good fluidity, compaction and high density.
Fine-grained powder (1-10 microns): usually used for high-precision, high-strength parts or parts with complex shapes. This type of powder can improve the density after sintering, but the fluidity is poor and the process is more difficult.
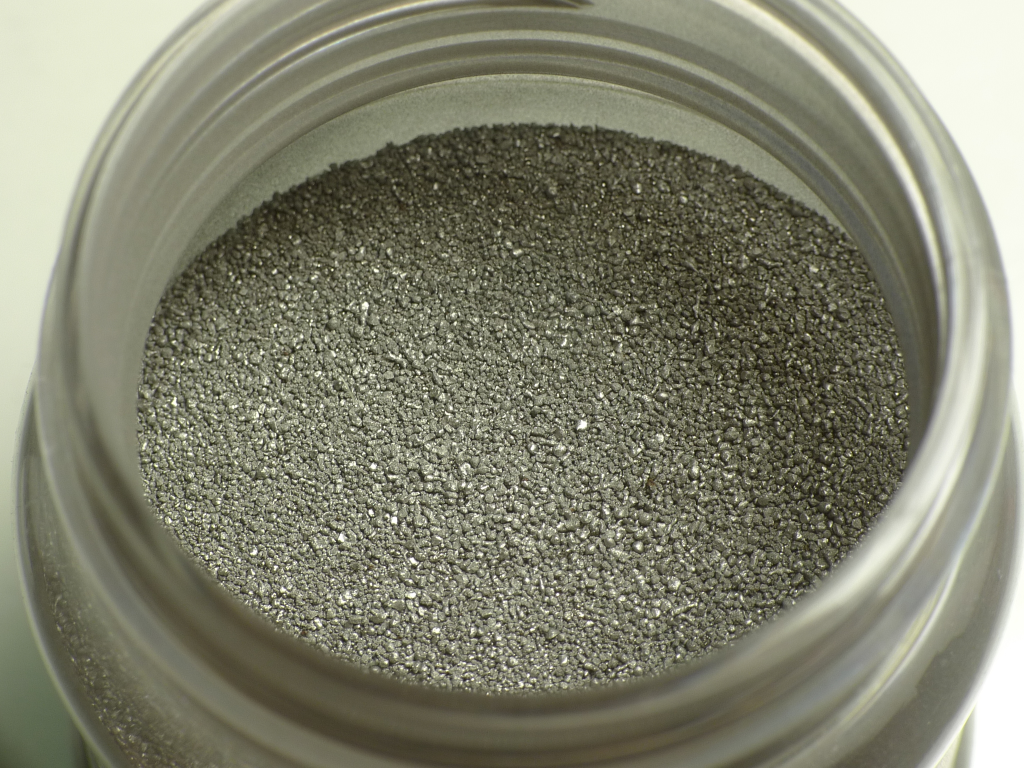
2. The effect of particle size on the process
In the pressing process. Metal powders with larger particle sizes show excellent fluidity, which is convenient for mold filling and effectively improves the molding efficiency. However, larger powder particles may cause the porosity of the finished parts to be high, thereby weakening its density. For parts that pursue high-strength performance, the use of fine-grained powder becomes a better choice, which can significantly improve the density and strength of the parts.
In the metal injection molding (MIM) process. It is usually required to use fine powders with a particle size range of 5-20 microns to ensure that the powder and binder can be evenly mixed to achieve high-precision injection molding. The use of fine powder can optimize the sintering density of parts and improve the mechanical properties of the final product. However, this also brings process challenges, such as the need for higher molding pressure and more sophisticated sintering process control.
3. The effect of particle size on performance
Density and strength: fine-grained powder can show better sintering performance in the sintering process, thereby improving the density and strength of parts, which is particularly suitable for manufacturing high-precision and complex parts. In situations where parts need to have wear resistance, corrosion resistance or high strength, it is particularly important to use fine-grained powder.
Porosity and permeability considerations: In contrast, larger powder particle sizes often result in higher porosity in sintered parts, which is advantageous in certain specific applications, such as the preparation of filter materials or the manufacture of parts requiring high permeability.
Flowability and filling characteristics: Generally speaking, the increase in powder particle size helps to improve its flowability, which is of great benefit to the smooth filling and molding process of the mold. However, fine-grained powder is slightly insufficient in flowability and is prone to blockage or uneven filling in the mold, so special attention must be paid and proper handling must be made during processing.
4. Particle size selection in application scenarios
Automotive parts: In the automotive manufacturing industry, powder metallurgy parts often use powder materials with a medium particle size range (10-50 microns) to achieve ideal density while simplifying the production process, such as the manufacture of key components such as gears and bearings.
High-precision electronic components: For micro-transmission components or conductive elements in electronic devices, fine-grained powders (1-10 microns) are indispensable to ensure that the excellent precision and strength of the final product meet stringent requirements.

Filter media manufacturing: When producing materials that require air permeability or filtering functions, it is more ideal to use larger particle size powders (50-150 microns) because it can effectively build the required pore structure and improve the filtration performance of the material.
5. Particle size measurement and control
Powder particle size is usually measured using laser particle size analyzers, sieving methods or microscopy techniques. For high-precision powder metallurgy applications, it is crucial to strictly control the distribution of powder particle size to ensure consistent product performance during production.
The particle size of metal powder plays a key role in powder metallurgy, directly affecting the molding process, sintering process, and the mechanical properties and quality of the final product. Coarse-grained powders are suitable for materials that require high permeability, while fine-grained powders are suitable for high-precision, high-strength parts manufacturing. High-precision processes such as MIM usually require finer powders to achieve the required density and mechanical properties.