Against the background of the rapid development of the power tool industry, there is an increasing demand for high-performance, durable and affordable parts. Powder metallurgy (PM) technology is gradually emerging as an innovator in this field. The unique properties of metal powders allow manufacturers to create parts that meet the demanding standards of modern power tools. This article will delve into the unique advantages of powder metallurgy in power tool components and highlight its key applications.
Powder metallurgy, simply put, is a process of manufacturing solid metal parts by pressing and sintering metal powder. This technology allows manufacturers to precisely control the density, strength and dimensional accuracy of the final product, and is particularly suitable for producing complex shapes and designs that are difficult to achieve with traditional processing methods.
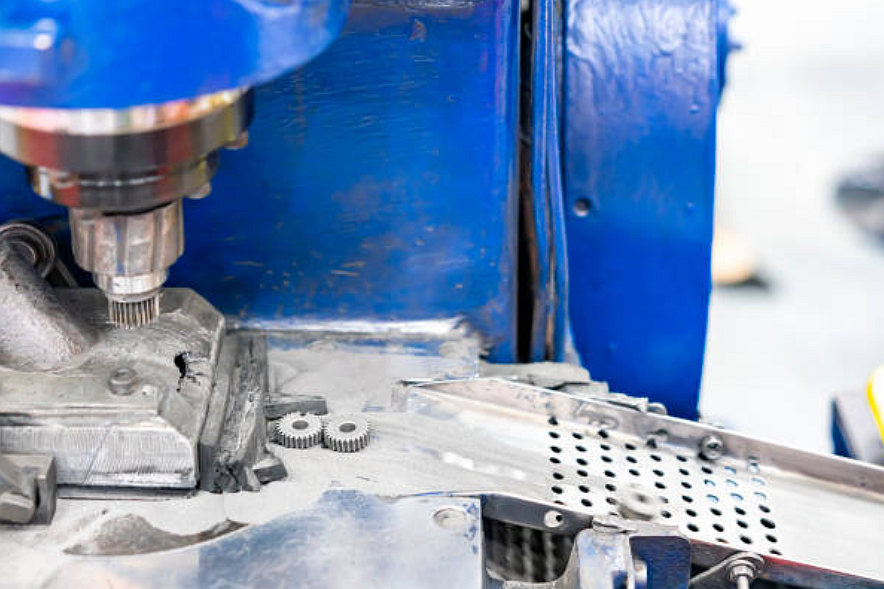
In the field of power tools, powder metallurgy shows significant advantages.
First, from a cost-effectiveness perspective, powder metallurgy significantly reduces material waste through near-net shape production and reduces the need for extensive machining, thereby effectively controlling production costs.
Second, parts manufactured through powder metallurgy often have superior mechanical properties, such as higher strength, hardness, and wear resistance, which are critical for frequently used power tools.
Additionally, powder metallurgy offers design flexibility, allowing manufacturers to create custom parts with internal cooling channels or complex geometries to meet specific tooling requirements.
Finally, PM components can also be optimized for power tool performance, such as by customizing porosity to enhance lubrication retention, thereby improving performance and service life in high-speed applications.
In power tools, the application of powder metallurgy is widespread and critical. Gear components are an important part of this. Powder metallurgy technology can produce high-precision and high-strength gears to ensure effective power transmission and long life of power tools such as electric drills and saws. In addition, components such as the stator and rotor in electric motors also benefit from powder metallurgy technology, which ensures that the motor performs optimally in the application by producing complex-shaped and high-density components to provide the required power and efficiency.
Cutting tools produced by powder metallurgy have also attracted much attention. Their high hardness and wear resistance allow the tools to maintain longer service life and sharpness under challenging conditions. At the same time, powder metallurgy is also used to make housings and protective cases for power tools. These parts are designed to be both lightweight and strong, providing protection while reducing the overall weight of the tool.
As the power tool market continues to grow and develop, powder metallurgy is becoming increasingly important as a key technology for producing high-quality components. With its cost-effectiveness, design flexibility and enhanced mechanical properties, powder metallurgy is changing manufacturers’ strategies in the production of power tool components.
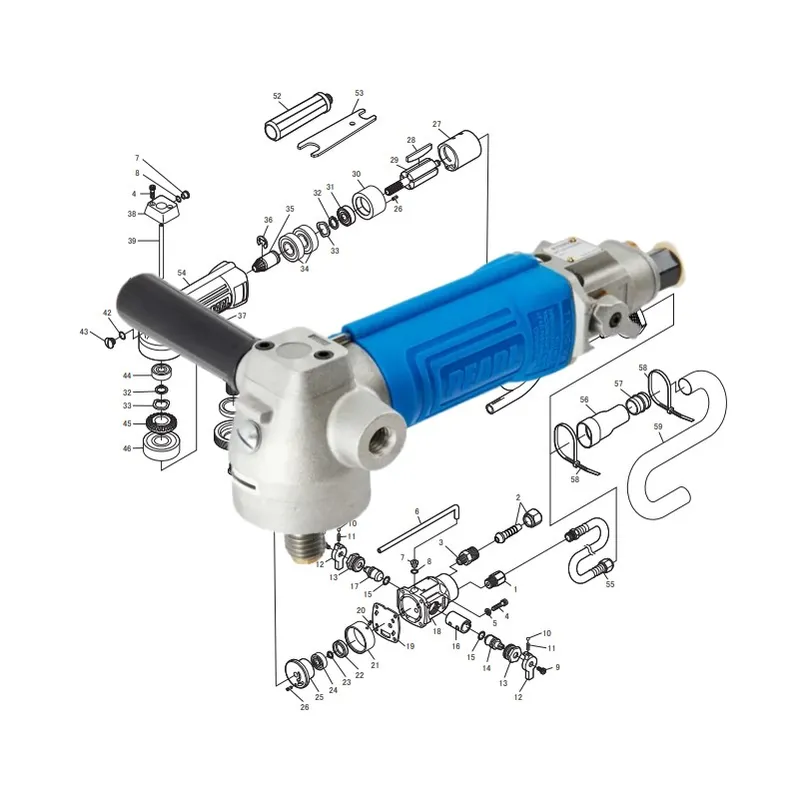
Shenzhen Yujiaxin Technology Co., Ltd., as a leader in the field of powder metallurgy, specializes in the preparation, forming, and sintering of metal powders, committed to providing high-quality powder metallurgy products. We employ advanced atomization techniques to ensure uniform particle size and high purity of the metal powders, laying a solid foundation for subsequent pressing and sintering processes. Through precise mold design and optimization, we achieve one-time forming of complex-shaped parts, significantly enhancing production efficiency and product accuracy. During the sintering process, we utilize high-temperature vacuum furnaces to precisely control the sintering curve, ensuring material densification and optimal performance. Our powder metallurgy products, distinguished by their excellent mechanical properties, good dimensional stability, and cost-effectiveness, are widely used in various industries including automotive, aerospace, electronics, and more.