Gear parts, with their excellent precision and complex geometric structure, play a core role in many fields such as automobile manufacturing, medical equipment, consumer electronics, etc. However, in the MIM (powder injection molding) process, the deformation of parts after sintering, especially for gears with extremely high dimensional accuracy requirements, even a small deformation will have a profound impact on their meshing accuracy and transmission efficiency.
This paper aims to deeply explore the causes, correction strategies and practical cases of sintering deformation of gear parts, and provide an effective solution to this problem.
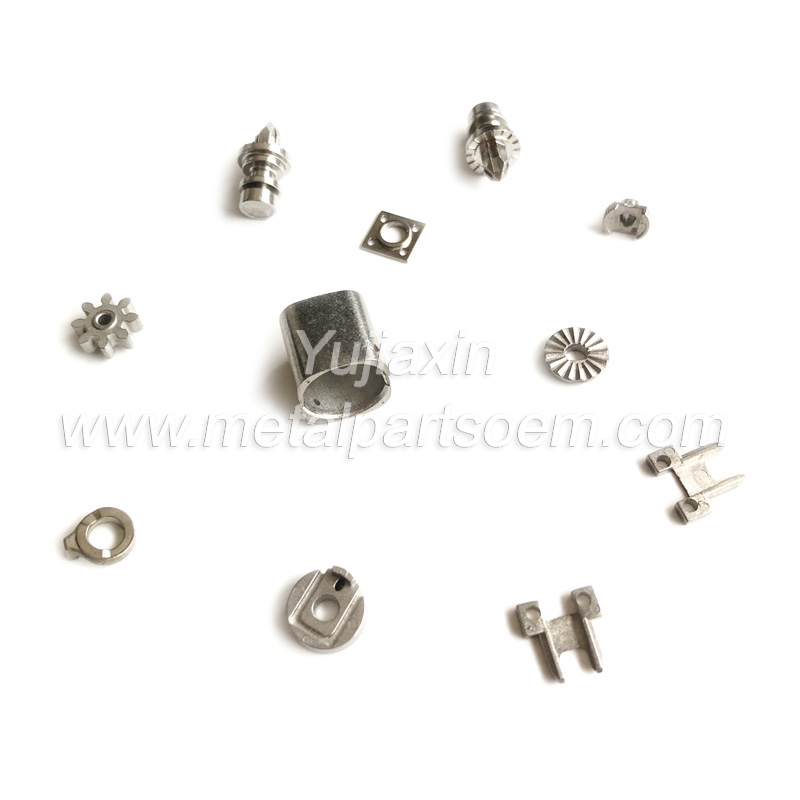
The deformation phenomenon after sintering mainly includes uneven radial shrinkage, axial warping and distortion of tooth shape. The root causes of these deformations are often closely related to material properties, process parameter settings and mold design. For example, the uneven distribution of metal powder particle size will cause shrinkage differences during sintering, and the unreasonable binder ratio may leave residual stress in the degreasing stage. In addition, the loss of control of sintering temperature or the imbalance of cooling rate will aggravate the accumulation of thermal stress, thereby inducing deformation. The lack of compensation mechanism or uneven distribution of demolding force in mold design has laid hidden dangers for deformation.
For the above deformation problems, the correction methods are mainly divided into three categories: heat treatment correction, mechanical correction and mold compensation design.
1. Heat treatment correction.
By heating to the softening temperature of the material and applying fixture pressure, parts with large dimensional deviations can be effectively corrected. It is suitable for mass production, but has strict requirements for fixtures and process control.
2. Mechanical correction
It is more suitable for repairing small batches or local deformations. Through manual adjustment or the use of correction equipment, the design form of the parts can be quickly restored.
3. Mold compensation design
Preventing deformation from the source can balance the stress distribution during the sintering stage and greatly reduce the risk of deformation. For example, using finite element analysis to predict the deformation trend after sintering and optimizing mold parameters through multiple experimental iterations can significantly improve the stability of production and the quality of parts.
At the process optimization level, precise control of heating and cooling curves is the key. Slow heating process helps to reduce the concentration of thermal stress, while uniform cooling can prevent deformation of parts caused by temperature differences. In addition, the selection of metal powder with uniform particle size distribution and the adjustment of material formula are also crucial to improving the stability of part sintering. For parts that require extremely high precision, the appropriate introduction of reinforcing materials such as ceramic fiber can further enhance the dimensional control ability.
Taking a domestic new energy vehicle gearbox gear as an example, the part had uneven outer diameter shrinkage after sintering, resulting in unsatisfactory meshing effect. After in-depth analysis, it was found that the main reasons were the inadequacy of mold compensation design and the lack of precision in sintering process control. By adjusting the compensation value of the mold outer diameter size and optimizing the sintering temperature and holding time, the customer finally greatly increased the part qualification rate from 80% to 98%. This systematic correction strategy not only solves the current deformation problem, but also points out the direction for subsequent production optimization.
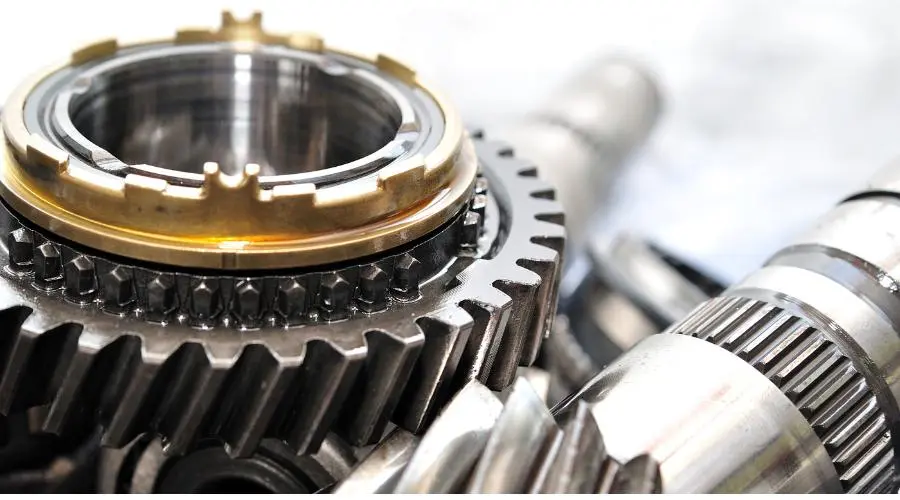
In summary, although the deformation problem of gear parts in MIM injection molding is complex, it can be fully achieved through in-depth cause analysis, scientific correction practice and continuous process optimization. Choosing a suitable correction method and focusing on preventive measures at the source will be the key to overcoming this problem.
Shenzhen Yujiaxin Technology Co., Ltd. is a leader in the field of metal injection molding (MIM). We focus on providing excellent metal parts solutions for the medium and high demand markets. Relying on advanced MIM technology, we can accurately process metal parts with complex structures, extremely high precision and stable performance, which are widely used in high-end fields such as communications, medical, automobiles, aerospace, etc. Yujiaxin adheres to the spirit of craftsmanship and continuously optimizes the process to ensure that each product can meet the most stringent quality standards of customers. We are committed to becoming a trusted partner of our customers, jointly promoting industrial upgrading, and opening a new chapter in metal parts processing.