In the field of metal injection molding (MIM) and powder metallurgy production, the appearance quality of parts is not only the focus of customers, but also a key yardstick for measuring the stability of production processes and product reliability. However, due to the complexity of the process, appearance defects occur from time to time, which has become a major challenge in the production process. Next, through this blog, I will discuss with you several common appearance defects, the reasons behind them, and practical solutions.
1. Rough surface: a stumbling block in the process journey
If the surface of the part appears rough and uneven, it will not only affect the visual beauty, but also may weaken its overall performance. This is usually due to uneven powder particle size, poor mold quality or improper injection parameters.
Improvement method:
- Choose finer and more uniform powder raw materials to ensure a solid material foundation.
- Carefully adjust the injection pressure and speed to allow the material to flow freely in the mold to form a smooth surface.
- Regular cleaning and polishing of the mold is essential, because the “appearance” of the mold directly determines the “face” of the part.
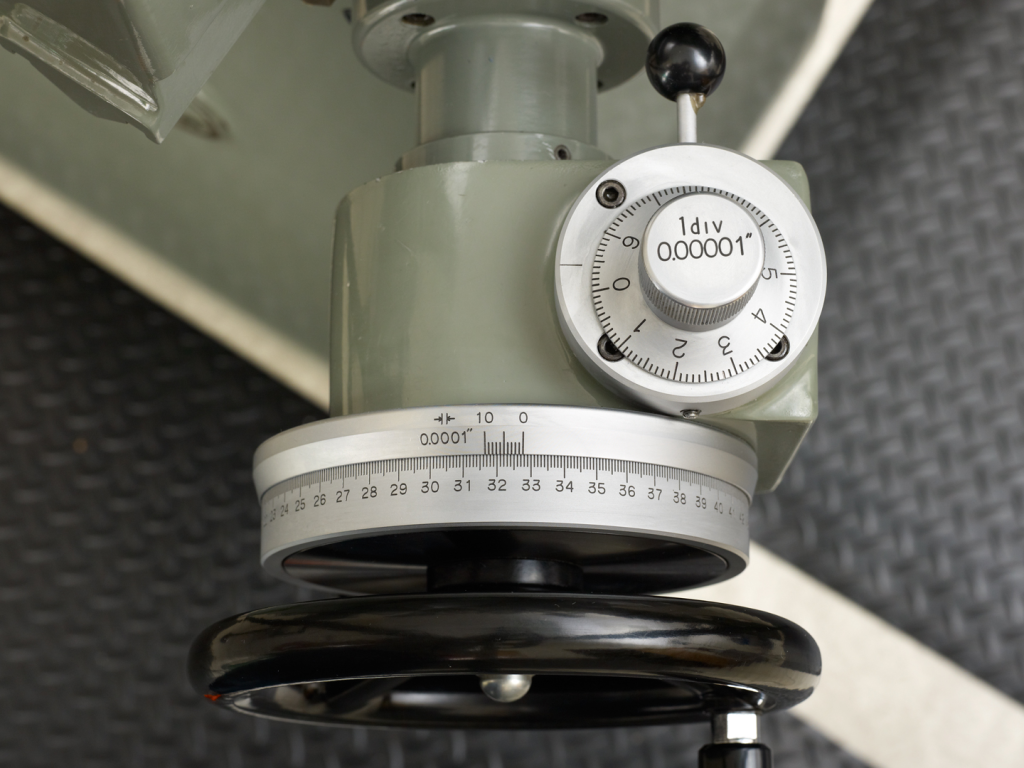
2. Uneven shrinkage: an invisible threat to precision
If the sintered parts are uneven in size or deformed, it may be caused by uneven material mixing, too high sintering temperature or unreasonable mold design.
Improvement method:
- Ensure that the powder and binder are fully mixed to reduce internal stress
- Accurately control the heating rate and holding time during sintering, and treat each product like a treasure.
- Consider the uniformity of wall thickness when designing the mold to ensure that the parts remain stable during the sintering process.
3. Cracking: a hard flaw that cannot be ignored
Cracks that appear in parts during degreasing or sintering are often caused by the accumulation of internal stress or the influence of residual gas.
Improvement method:
- Carry out degreasing treatment in stages, starting from low temperature and gradually releasing internal stress.
- Ensure that the degreasing process is thorough, especially for parts with complex shapes, to ensure that the gas exhaust channel is unobstructed.
- Improve the injection process to avoid uneven filling and ensure the integrity of the internal structure of the parts.
4. Deformation: Accidents during sintering
If parts bend or deform after sintering, it may be caused by excessive temperature or insufficient support.
Improvement methods:
- Adjust the sintering curve to find the most suitable temperature range.
- Use sintering fixtures to provide support for complex parts to ensure that they maintain a stable shape in a high temperature environment.
- Optimize the mold demolding design to reduce shape deviation caused by stress concentration.
5. Black spots or spots: surface defects
These defects may be caused by material oxidation, mold contamination or impurities. Although small, they affect the overall appearance.
Improvement methods:
- Use high-purity powder raw materials to avoid oxidation and impurity contamination.
- Clean the mold regularly and strictly control the amount of release agent used.
- Improve the production environment, reduce the interference of dust and foreign matter, and keep the production area clean.
6. Color difference: the individuality of the process
The inconsistent color of the sintered parts is usually due to uneven material composition or improper control of the sintering atmosphere.
Improvement methods:
- Ensure that the raw materials are mixed evenly to make the parts consistent inside and outside.
- Adjust the sintering atmosphere, such as using a reducing atmosphere, to avoid excessive oxidation reaction.
- Regularly update the injection material to avoid performance fluctuations caused by material aging.
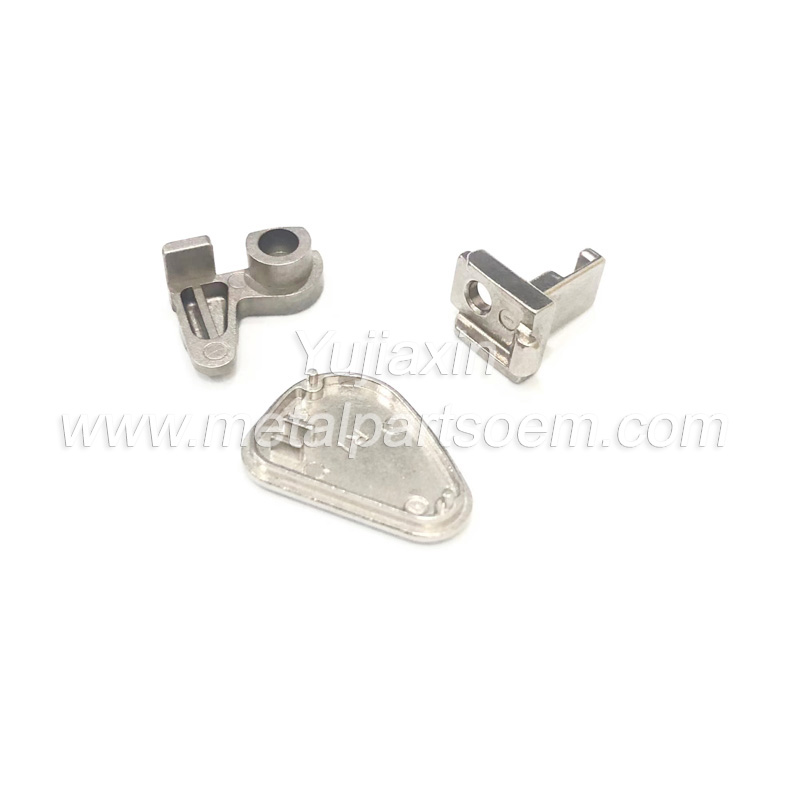
7. Flash: unnecessary troubles
Flash is the direct result of poor mold closure or excessive injection pressure, which increases the difficulty of subsequent processing.
Improvement method:
- Regularly inspect the mold to ensure tight and seamless closure.
- Adjust the injection pressure to the optimal value to ensure complete filling without overflow.
Shenzhen Yujiaxin Technology Co., Ltd., driven by innovation, uses cutting-edge titanium alloy metal powder injection molding technology to carefully create various medical devices and medical implant parts. We are committed to providing high-precision and high-reliability products to ensure the health and safety of every patient. Whether it is a complex pacemaker or a tiny dental implant, we can manufacture it accurately and perfectly match it. Choose Yujiaxin, choose trust and peace of mind.