Plating:
Plating is a surface covering where metal is deposited onto a conductive surface. Plating can be used to inhibit corrosion, improve solderability, harden, improve wear resistance, reduce friction, improve paint adhesion, change conductivity, or for radiation shielding.
Aerospace plating is essential to the survival and growth of the industry. Reliability, precision, and using the right materials are essential.
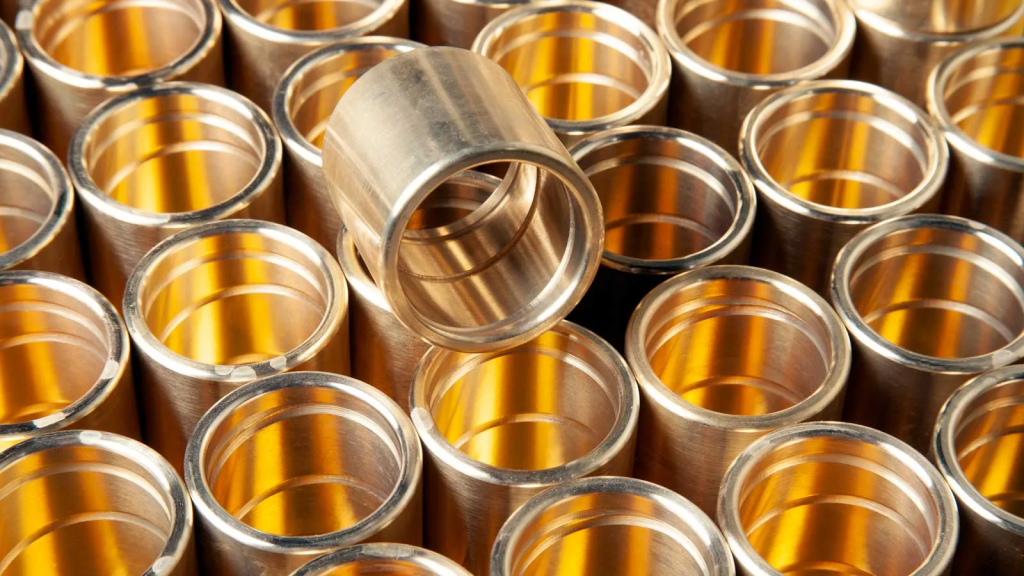
Painting:
As with any type of painting, applying a wet coat of paint to the metal surface is a necessity for metal painting. Typically, manufacturers use pumps, sprayers, or pressurized containers to ensure that the paint is evenly applied.
Polishing and Sanding:
Polishing involves scraping away surface material in order to achieve a better finish and prepare it for polishing. Polishing produces a high gloss, sometimes called a mirror effect, and smooths the surface.
Sandblasting:
With sandblasting, you can easily combine cleaning and finishing into one procedure. To achieve the necessary cleanliness and surface profile, abrasive particles are sprayed at high pressure onto the metal surface during sandblasting. Abrasives such as sand, glass, plastic, and aluminum oxide are used in this technique.
Black Oxide:
Black oxide is a conversion coating applied to iron, zinc, steel, stainless steel and copper. It gives a black, smooth finish and improves corrosion and wear resistance. Black oxide is commonly used as a surface treatment for a variety of industrial and commercial applications, including automotive and aerospace components, machinery and tools.
· Fasteners, hardware and tools.
· Automotive and aerospace components, black oxide is used as a surface treatment for a variety of parts, including engine components, defense parts.
Manganese Phosphating:
Manganese phosphating is well known as a wear protection measure and is widely used in the automotive/aerospace/defense industries. It is widely used to improve the sliding properties of engines, gears and power transmission systems. It has the highest hardness and superior corrosion and wear resistance to general phosphate coatings. Among other industries, manganese phosphating coatings are used in almost all metalworking industries to improve corrosion resistance.
Galvanizing:
Galvanizing is the process of covering a base metal (such as steel and iron, etc.) with a layer or coating of zinc to protect the base metal from corrosion.
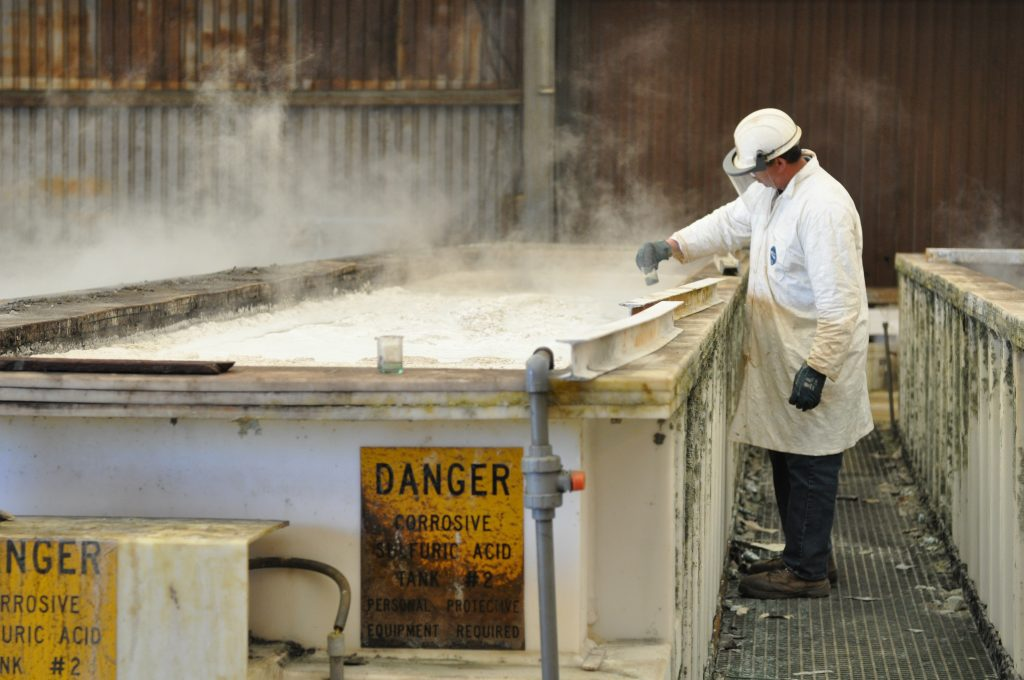
Anodizing:
Anodizing is a simple electrochemical process that coats aluminum surfaces with a protective layer of aluminum oxide. The thickness of the anodic coating applied determines the life of the surface.
Aluminium oxide is tough, resilient and weather resistant and protects the base metal. The coating may have a tinted hue or appear bronze due to the diffraction effect created by the coating.
Shenzhen Yujiaxin Technology Co., Ltd., since its inception, has been dedicated to the research and development of Metal Injection Molding (MIM) technology. The company boasts a high-quality technical team that leverages advanced production equipment and exquisite craftsmanship to provide clients with one-stop MIM solutions. From product design, mold development, material selection to mass production, Yujiaxin Technology strictly controls every step to ensure high precision and quality of its products. The company’s main products include, but are not limited to, injection-molded parts made of stainless steel, titanium alloys, copper alloys, and other metals, which are widely used in various fields such as automotive, medical, electronics, and communications. Through continuous innovation and optimization, Yujiaxin Technology has become a leader in the metal injection molding processing industry, earning widespread praise from domestic and international clients.