The medical industry, as the forefront of technological advancements, is always committed to improving patient care and enhancing medical standards through innovative technologies. In recent years, Metal Injection Molding (MIM) technology has emerged as a prominent force in the manufacturing of medical equipment, surgical instruments, and tools, thanks to its unique advantages.
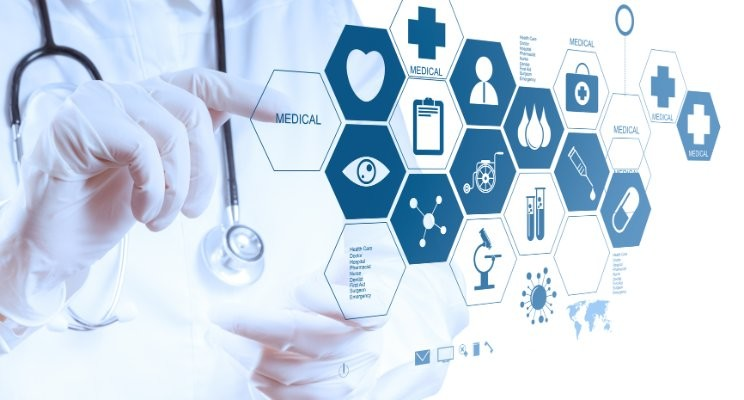
MIM technology is an advanced manufacturing process that combines the benefits of powder metallurgy and plastic injection molding. It enables the mass production of complex, high-strength metal components with excellent mechanical properties, such as high strength, hardness, good wear resistance, and corrosion resistance. These components achieve precise tolerance control, ensuring product stability and reliability. Furthermore, MIM technology offers a wide range of material choices, including stainless steel, titanium alloys, and cobalt-chromium alloys, meeting the diverse material needs of the medical industry.
The application of MIM technology is particularly significant in the medical field. Take surgical instruments as an example. Traditional machining methods often struggle with processing complex shapes and fine structures, while MIM technology can easily handle these challenges. Surgical instruments like forceps, scissors, and tweezers manufactured through MIM technology not only exhibit higher accuracy and consistency but also significantly shorten production cycles and improve production efficiency. For medical institutions, this means faster access to the required surgical instruments, thereby better serving patients.
In addition to surgical instruments, MIM technology also plays a crucial role in the manufacturing of medical equipment. For instance, it can be used to produce internal structural components, transmission parts, and connecting parts for medical equipment. These components need to withstand significant forces and pressures, requiring high material strength and wear resistance. Through precise powder blending and sintering processes, MIM technology can produce metal components that meet these requirements, ensuring the stability and reliability of medical equipment.
It’s worth mentioning that MIM technology also offers cost-effectiveness advantages. Compared with traditional machining methods, MIM technology can greatly reduce material waste and processing costs. Moreover, since MIM technology enables mass production, it can further lower the cost per unit product. For medical device manufacturers, this means creating a more streamlined supply chain without sacrificing quality, thereby enhancing market competitiveness.

Shenzhen Yujiaxin Technology Co., Ltd., as a leader in MIM technology, fully understands the importance of this technology in the medical industry. The company not only possesses advanced MIM production equipment and a skilled technical team but also strives to apply MIM technology to more medical products. Through continuous research and innovation, Yujiaxin Technology has successfully applied MIM technology to the manufacturing of products such as surgical forceps, endoscopic forceps, and ultrasonic scalpel blades, achieving remarkable results.
Looking ahead, with the continuous development of the medical industry and the increasing demand for high-quality, efficient manufacturing technologies, MIM technology will play an even more crucial role in the medical field. Shenzhen Yujiaxin Technology Co., Ltd. will continue to adhere to the principles of innovation, quality, and service, providing the medical industry with more high-quality, efficient MIM solutions to drive its sustained development.