Powder metals are alloys that are processed into fine, granular powders through one of a variety of processes. These metals are primarily made of stainless steel, brass, copper, iron, or bronze and can be blended with other alloys to achieve the material properties and characteristics required for a specific application. Powder metal parts offer greater flexibility in material use and mechanical properties, can be highly customized and easily replicated, while producing high-strength, cost-effective components.
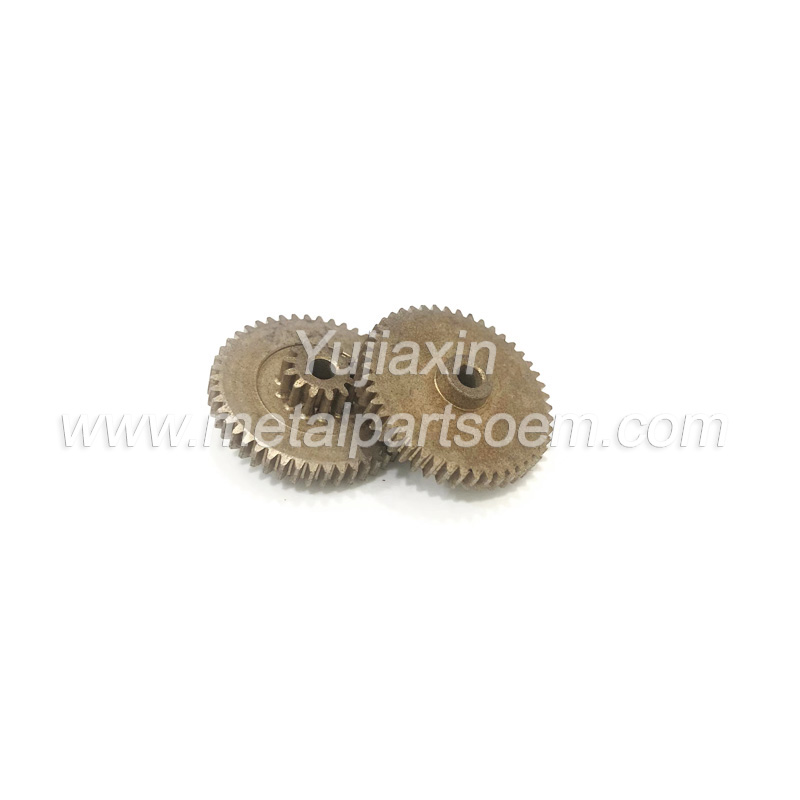
Making High-Strength Components
Powder metallurgy (PM) refers to a manufacturing process that forms powdered metal or metal mixtures into desired specifications through a unique combination of heat and compression, resulting in parts and components that are stronger than traditional forging processes.
The process is shorter than other manufacturing techniques, and the main steps include the following:
1. The metal is made into powder through chemical treatments such as solid-state reduction, atomization, electrolysis, or oxide reduction and thermal decomposition.
2. The powder is mixed with other metals, alloying agents, and lubricants to reduce friction, increase flow, and produce a homogenous mixture, which is then fed into a rigid tooling set for processing.
3. The metal mixture is compressed into the appropriate geometry using dies, punches, hydraulic presses, or other consolidation measures.
4. The compacted fragments are sintered in a controlled atmosphere, using extremely high temperatures to metallurgically bond the particles.
5. Secondary operations are performed on the parts, depending on the requirements of the end application.
The PM process is considered environmentally friendly because it produces harmless nitrogen and hydrogen byproducts, while also limiting production waste by utilizing more than 97% of the material entering the process.
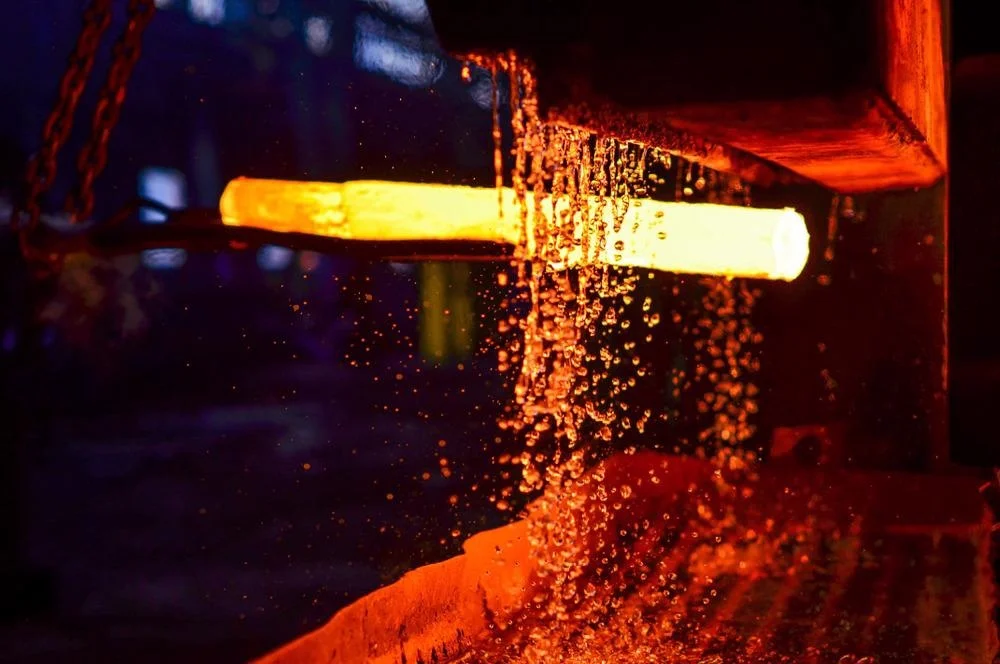
Heat Treatment and Finishing Options
After sintering, parts may undergo additional heat treatment or finishing to increase material strength and hardness, improve corrosion resistance, improve part tolerances, enhance surface finish, etc.
Secondary operations include the following:
· Heat treatment: quenching, tempering, steam treatment, furnace welding, etc.
· Machining: drilling and tapping, turning, milling or grinding
· Impregnation: oil or resin
· Finishing: deburring, tumbling, polishing, coating or plating, welding, etc.
Shenzhen Yujiaxin Technology Co., Ltd. has been specializing in the field of metal powder metallurgy processing since its establishment, dedicating itself to the research and development of the entire chain technology including metal powder preparation, forming, sintering, and post-treatment. Leveraging advanced Metal Injection Molding (MIM), Powder Metallurgy Pressing (PM), and Powder Metallurgy Copper Infiltration techniques, the company provides high-precision, high-performance metal component solutions for various industries such as automotive, electronics, communications, and medical devices. Through continuous optimization of production processes, Yujiaxin Technology has significantly enhanced product density, hardness, and wear resistance, earning widespread recognition in the market.